Welding WPS Explained: Key Parts and Benefits for Your Welding Procedures
Welding WPS Explained: Key Parts and Benefits for Your Welding Procedures
Blog Article
Unlocking the Power of Welding WPS: Approaches for Effectiveness and Safety in Fabrication
In the world of construction, Welding Procedure Requirements (WPS) stand as the backbone of welding procedures, dictating the necessary actions for attaining both performance and safety in the manufacture process. Recognizing the complexities of WPS is paramount to utilizing its full possibility, yet several companies struggle to open real power that exists within these files (welding WPS). By diving right into the techniques that optimize welding WPS, a world of improved performance and increased safety and security waits for those happy to check out the subtleties of this essential aspect of fabrication

Relevance of Welding WPS
The significance of Welding Procedure Requirements (WPS) in the fabrication market can not be overemphasized. WPS function as a crucial roadmap that describes the needed actions to guarantee welds are done continually and correctly. By defining crucial parameters such as welding processes, products, joint layouts, preheat temperatures, interpass temperatures, filler metals, and post-weld warm therapy needs, WPS provide a standardized approach to welding that enhances effectiveness, high quality, and safety and security in fabrication processes.
Adherence to WPS helps in accomplishing uniformity in weld top quality, lowering the likelihood of flaws or architectural failings. This standardization additionally helps with compliance with industry regulations and codes, ensuring that produced frameworks fulfill the called for safety and security criteria. In addition, WPS documents makes it possible for welders to reproduce effective welding treatments, bring about constant results across various jobs.
Essentially, the meticulous advancement and stringent adherence to Welding Procedure Specs are critical for supporting the integrity of welded frameworks, guarding versus prospective threats, and promoting the online reputation of manufacture firms for providing premium services and products.
Trick Components of Welding WPS

Enhancing Performance With WPS
When enhancing welding procedures, leveraging the crucial elements laid out in Welding Procedure Specs (WPS) comes to be vital for maximizing and simplifying procedures efficiency. One means to enhance performance with WPS is by very carefully picking the appropriate Read Full Report welding criteria. By sticking to the specific standards supplied in the WPS, welders can ensure that the welding equipment is established correctly, bring about high-grade and regular welds. In addition, adhering to the pre-approved welding sequences described in the WPS can significantly minimize the time invested on each weld, ultimately raising total efficiency.
Consistently examining and updating the WPS to include any kind of lessons found out or technical improvements can also add to effectiveness improvements in welding procedures. By embracing the standards set forth in the WPS and constantly seeking methods to maximize procedures, fabricators can attain higher performance levels and premium end results.
Ensuring Security in Manufacture
Guaranteeing safety in manufacture entails a diverse approach that includes various elements of the welding procedure. Welders have to be equipped with proper gear such as safety helmets, handwear covers, and protective clothes to mitigate threats connected with welding activities.
Additionally, adherence to correct ventilation and fume extraction systems is critical in keeping a healthy job atmosphere. Welding fumes have hazardous compounds that, if breathed in, can pose significant health official statement and wellness risks. Carrying out effective air flow steps helps to lessen exposure to these harmful fumes, promoting breathing health among employees.
Normal equipment maintenance and examinations are also essential for making certain safety in manufacture. Defective machinery can cause injuries and accidents, highlighting the significance of prompt repair services and regular checks. By prioritizing precaution and promoting a culture of understanding, fabrication facilities can produce a secure and effective job atmosphere for their employees.
Applying WPS Finest Practices
To enhance functional performance and ensure high quality outcomes in manufacture procedures, integrating Welding Procedure Specification (WPS) ideal methods is critical. Choosing the suitable welding process, filler material, and preheat temperature level defined in the WPS is crucial for attaining the desired weld quality. Making sure that certified welders with the needed qualifications lug out the welding procedures according to the WPS guidelines is crucial for uniformity and reliability.
Conclusion
To conclude, welding WPS plays a vital function in guaranteeing performance and safety and security in fabrication procedures. By concentrating on vital elements, enhancing performance, and applying best practices, business can maximize their welding procedures. It is important to prioritize safety and security procedures to avoid mishaps and ensure a smooth production procedure. By adhering to these techniques, organizations can unlock the full capacity of welding WPS in their manufacture operations.
In the realm of manufacture, Welding Treatment Requirements (WPS) stand as the foundation of welding procedures, determining the essential steps for achieving both performance and safety in the construction process. By specifying important specifications such site web as welding procedures, products, joint layouts, preheat temperatures, interpass temperatures, filler steels, and post-weld heat treatment requirements, WPS give a standardized method to welding that improves effectiveness, quality, and safety and security in manufacture processes.
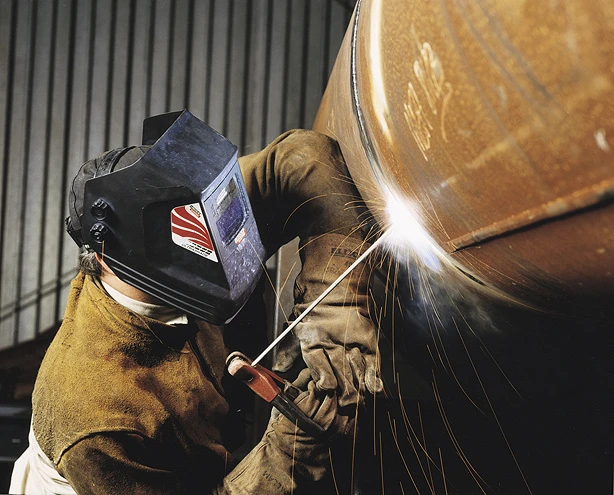
When maximizing welding procedures, leveraging the crucial components detailed in Welding Procedure Specs (WPS) comes to be important for streamlining processes and making the most of efficiency. (welding WPS)
Report this page